WGM The Wind Generator Vibration On-line Monitoring System
WGM apply to wind power generators of spindle bearing, gear box bearings, gears and generator bearing vibration monitoring and analysis
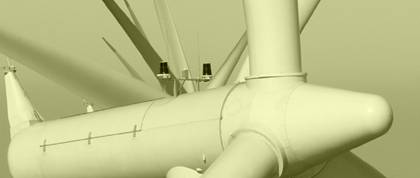
Wind power generators are usually better than other kinds of electric power equipment more vulnerable to vibration. Electric power company of new fan transmission system live longer expectations is becoming more and more high, high efficiency energy conversion, synchronous generators, permanent magnet motor, two class above the planet round with the former stage or hydraulic gearbox is the focus of concern. WGM system help users understand the key parts of the wind generator running state information. Wind power generators in reaching the rated power, the axis of rotation speed only 10 to 30 RPM, low speed rotating components impact signal amplitude is very small, the traditional hardware demodulation analysis method is invalid. Basic WGM equipped with high performance data collector, can provide high precision, long time data collection ability; At the same time the upper analysis software provides unique gPK digital demodulation technology, through the technology to detect the impact of the signal is very weak, suitable for low speed bearings (such as wind damage detection of the main bearing). Due to the change of the wind, the wind power units will be in operation speed and load changes, this led to the traditional spectrum analysis technology cannot be used, WGM transient rotation speed tracking based on the order of the analysis technology, which can eliminate the speed fluctuation of influence on the result of the analysis. Adopt international standard variable condition of under the circumstance of wind generator vibration state to the quantitative evaluation, convenient quickly understand the health status of vibration.
• Vibration data analysis;
• Automatic condition assessment;
• Intelligent statistical analysis;
• Statements automatic generation.
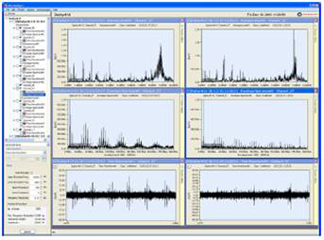
Input signal channel | max. 8 Vibration channel + 1 Synchronous channels |
ICP constant current power supply | 3.6mA@42V |
Measuring parameters | Acceleration, speed, displacement |
Measurement type | Spectrum diagram, time domain waveform, phase, the RMS, peak, the peak-peak |
Input signal range | ±40V |
Automatic range function | Yes |
A/D-16bit dynamic range | > 90 dB |
Frequency range | Max.40kHz |
High-pass filter | Set range 0.5Hz...20kHz |
Low-pass filter | Set range 0.1Hz...40kHz |
Sampling frequency | Max. 102.4kHz |
FFT resolution | 400...56020 line(single chanel) |
Sampling length | Longest 3Mbytes per sight,60sec@25.6kSPS |
Speed input | Signal range:±40V, sensor power supply: +5Vn |
Measurement range | 0.1Hz...1000Hz |
Operating system | Windows XP/ Windows Vista/ Windows 7 |
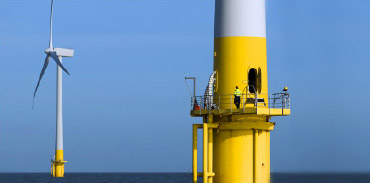
Offshore wind farm
Working with Enxco's wind turbine unit, Sigmatech is at the forefront of the new millennium in power generation. Enxco's wind turbine electrical solutions are designed to meet UL and CSA standards and to withstand harsh climates. Enxco's components increase reliability in the nacelle's control systems and in the base of the turbine's tower.